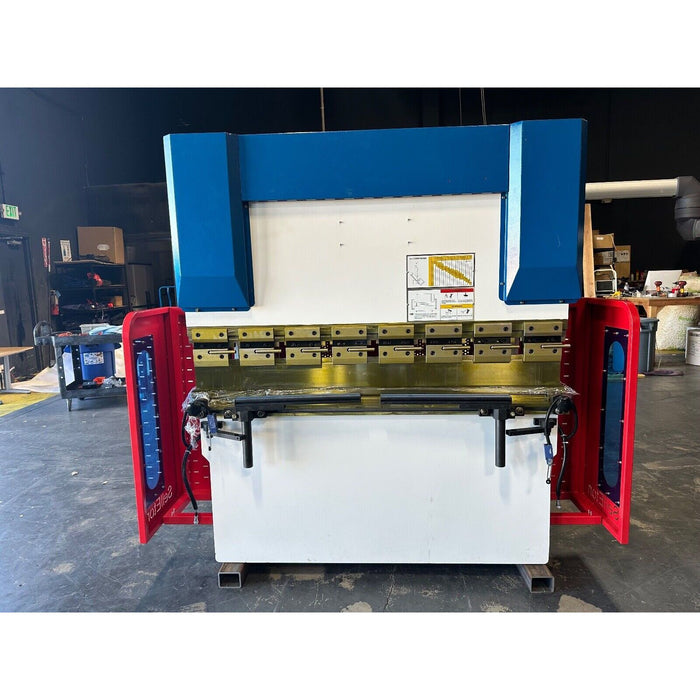
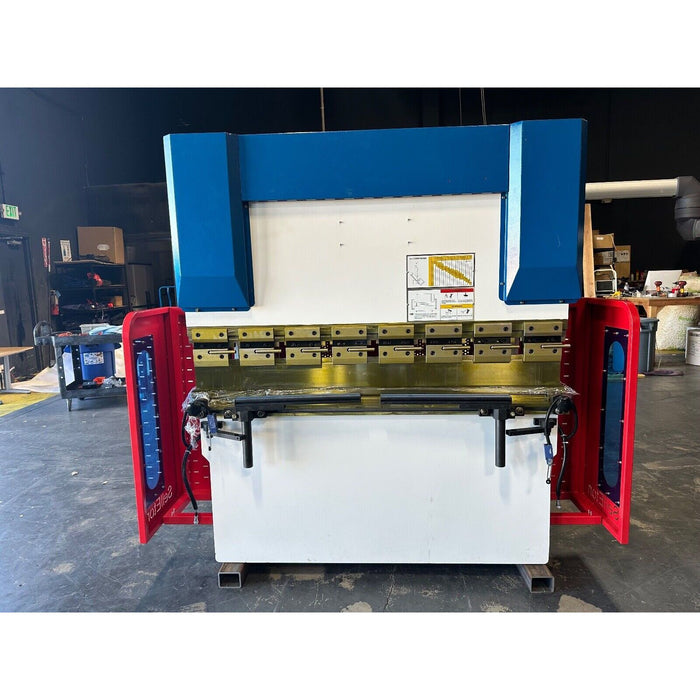
Are you searching for a solution to effortlessly bend and form large, heavy metal sheets with unmatched precision?
The SellEton SL-33-TON-5PB Sheet Metal Bending & Forming Machine is your definitive answer. Engineered to manage the complexities of substantial metal bending tasks, this powerhouse combines brute strength with advanced technology, ensuring your projects meet the highest standards of accuracy and quality.
Key Benefits:
- Powerful Bending Capability: Leverage a 33-ton pressure capacity over a 63-inch worktable to manage extensive and robust metal bending operations.
- Consistent Output: Equipped with a potent 7.5 hp motor and a 220V, 3-phase electrical setup, ensuring reliable and steady performance.
- Advanced Programming: Features an Estun E21 2-axis controller for easy programming of up to 40 different programs, each with 25 step sequences.
- Precise Production Tracking: Built-in piece counter for accurate tracking of production output, ensuring efficiency and consistency in your projects.
- Superior Quality Components: Constructed with high-quality components from renowned manufacturers like NOK, Siemens, and Omron for enhanced durability and performance.
- Enhanced Safety Measures: Comes with integrated light curtains to ensure operator safety during use.
- Versatile Tooling Options: Includes a comprehensive set of tools such as a 78-degree gooseneck punch and a multi-Vee bottom die for various bending needs.
Specifications at a Glance:
- Table Size: 63" x 7"
- Back Gauge Length: 21.5"
- Return Speed: 3.3" per second
- Throat Depth: 8"
- Stroke Distance: 3.15"
- Approach Speed: 3.5" per second
- Bending Speed: 0.394" per second
- Distance Between Housings: 51.25"
- Distance From Table to Ram: 13.325"
Investing in the SellEton SL-33-TON-5PB solves your metal bending challenges and enhances your operational efficiency and production quality. Feel the satisfaction of flawless execution and detailed precision with every project you undertake. This machine ensures that your workspace is optimized for safety and performance, making it a vital asset for those serious about achieving professional-grade metalworking results. Join the ranks of satisfied operators who have transformed their metal-forming capabilities with the SellEton SL-33-TON-5PB.
Please contact our sales team for more information or to discuss your specific requirements. We're here to help you find the perfect weighing solution for your industrial needs.
Free Shipping: Available across 48 continental USA. Extra charges may apply for residential, farm, or rural areas.
Express Shipping: Overnight and faster shipping options available at additional costs. Quotes obtainable via email.
Delivery Time: Typically 5 to 7 business days, varying by location and external conditions.
Tracking Information: Provided via email upon shipment. Accessible through account login. Additional information available upon request.
Return Policy: 15-day return period for unused, original condition products. A 25% restocking fee applies. Buyer covers original and return shipping costs.
Customer Support: Contact at (844)-735-5386 or info@selletonscales.com for queries or concerns about shipping.